Roll Recoating
ATS started refurbishment and recoating of rolls and components in steel plants. Rolls refurbishment involves grinding, stress relieving, Tungsten carbide coating, Ceramic coating, chrome plating and finishing processes. Over the years our surface modification services have covered rolls operating in all lines of Cold Rolling Mill, Hot Rolling Mill & Pellet plants. We have so far refurbished more than 2200 steel mill rolls.
Hard Chrome Plating
Hard Chrome plating is an electrolytic method of depositing Chrome for engineering applications, from a Chromic acid solution. Chrome plating on rolls is undertaken in specially designed baths using customized chemical solutions.
Deposits can be applied from .25 – 1,000 microns thickness for a wide range of applications. The thinner deposits being used to substantially increase the life of components in wear applications or corrosive environments, and the thicker deposits being used for salvage and repair of worn, damaged or mis-machined components.
- Low Friction
- Super finishing to Mirror Finishes
- Excellent Wear Resistance
- Good Corrosion Resistance
- 0.25 – 1,000 Micron Thick
Tungsten Carbide and Ceramic Coating
HP/HVOF coating systems mounted on robots are used to provide uniform and very dense Tungsten Carbide and Ceramic base coating on roll surfaces. These coatings are done in an acoustic spray booth.
As furnace rolls convey steel sheets in high-temperature environments, gripping property and build-up resistance are needed. ATS coatings meet various customers' needs with longer service life.
ATS coating is applied to CGL components to prevent the surface from corrosion and other.
Process Roll Coating:
- Bridle Roll
- Deflector Roll
- Steering Roll
- Looper Roll
- ACBR Roller
- Tensiometer Roll
- Flattner Roll
- Pass line Roll
Furnace Roll- CAPL & CGL
- Heating Section
- Soaking Section
- Slow Cooling section
- Nox Zone
- Boot roll
- Insitu Roll Profile measurement
POT Section
- Sink Roll
- Stabilizing Roll
- Snout
- Arm
- Sleeve & Bush
Grinding
We undertake grinding with precision CNC base roll grinders. Roll surfaces which have degraded due to various industrial wear factors are reground by precision roll grinders to restore original profile.
We measure the profile by a special Roll Profile instrument.
Our Grinding machines are capable to varies profile as below
- Flat Profile
- Taper Profile
- Single Crown Profile
- Double Crown Profile
- Camber profile
- Sine curve profile
ABRA-KOAT Coating
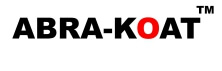
ABRAKOAT is an excellent replacement of traditional Hard Chrome plating with impermeable, hard and ductile coatings. Our patented ABRAKOAT coating has 3 times higher life than Hard Chrome Plating. These are very dense coatings with high bond strength more than 12000 psi which is more than double to HCP layer.
- High density with low porosity hence improved corrosion barrier
- Environmentally friendly alternative to Electrolytic Hard Chrome Plating
- Zero oxide content in the coatings
- Due to high surface hardness improved wear resistance
Roll finishing
Special grinding media, lapping and super polishing machines are used by our expert technicians to provide appropriate profile and surface finish to rolls as per customer requirements.
Make An Inquiry